17 May, 2019
STS in Stenungsund extends its cooperation with Scania and sees huge future potential in the truck sector

Ola Stalebo CEO
In the spring of 2018, Scandinavian Transmission Service AB (“STS”) in Stenungsund became a supplier partner to truck manufacturer Scania. STS was then commissioned to remanufacture planetary gears for Scania trucks. The planetary gears are included in “Scania Service Exchange,” an exchange concept whereby Scania sells remanufactured spare parts. The number of components in the system is growing steadily and has now resulted in an expansion of the cooperation between STS and Scania to also include rear axle gears. In March, STS began remanufacturing the first components on a new production line, where a dedicated Scania team is in charge of the work.
“Naturally, we are thrilled that Scania has chosen to extend our cooperation. Since we began remanufacturing planetary gears roughly a year ago, our relationship has become stronger, and we truly feel that Scania appreciates our work and the expertise of the STS employees in the Scania team. We also believe there is an opportunity to increase the investment and become a strong partner for other manufacturers of heavy commercial vehicles. Just like Scania, other companies are increasingly working according to the principle of a circular economy and establishing organisations and procedures aimed at remanufacturing power train components. This is opening up a market to us with huge growth potential,” says Ola Stålebo, CEO of STS.
Founded in 1969, STS is now celebrating its 50th anniversary as one of Europe’s leading companies in the industrial remanufacturing of transmissions and transmission components for passenger cars. The cooperation with Scania has initiated a long-term investment that may give STS a strong market position within the heavy commercial vehicle segment.
Customer-unique remanufacturing teams and production lines
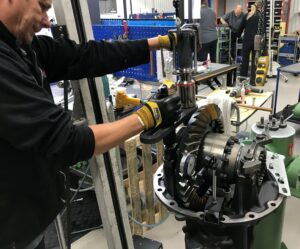
Assembly axle gear
“For decades, we have worked according to an industrial process philosophy governed by high requirements on quality, product finish and efficient flows. This, along with the expertise of our employees, was important to Scania when choosing a supplier partner. The fact that we also have the capacity to adapt our production to our customers is another strength, when we now invest in the future to widen our scope to other commercial vehicle manufacturers,” Ola Stålebo continues.
At STS in Stenungsund, special investments were made in the construction of production lines for Scania’s components. A major difference compared with components for passenger cars is that power train components for heavy vehicles are considerably larger and heavier, requiring special lifting systems and tools.
“Our strength lies in our committed and highly skilled employees and in having the capacity and space needed to adapt production lines to customers. By forming customer-specific teams with responsibility for various components, we create important leading-edge skills with high customer value,” Ola Stålebo explains.
According to Ola Stålebo, the need for remanufacturing is set to increase in the future. One reason is the circular economy and the desire among many manufacturers to introduce business ecosystems with the remanufacturing of various parts as a central part. There is also growing interest among owners of heavy vehicles to choose remanufactured components instead of new. A remanufactured replacement unit from STS has the same performance as a new product and is therefore a good choice for truck owners, both for financial and environmental reasons.
For more information, please contact:
Ola Stålebo, CEO, STS, +46 303 72 78 93, ola.stalebo@stsab.net